ORDERING
H. Theophile provides unparalleled service throughout the ordering process. Our sales team works closely with designers and architects in the specification and customization of hardware to complement their design vision. Showroom visits and samples can be arranged upon request. Upon project mobilization, H. Theophile will supply a technical submittal documenting the final designs and technical specifications.
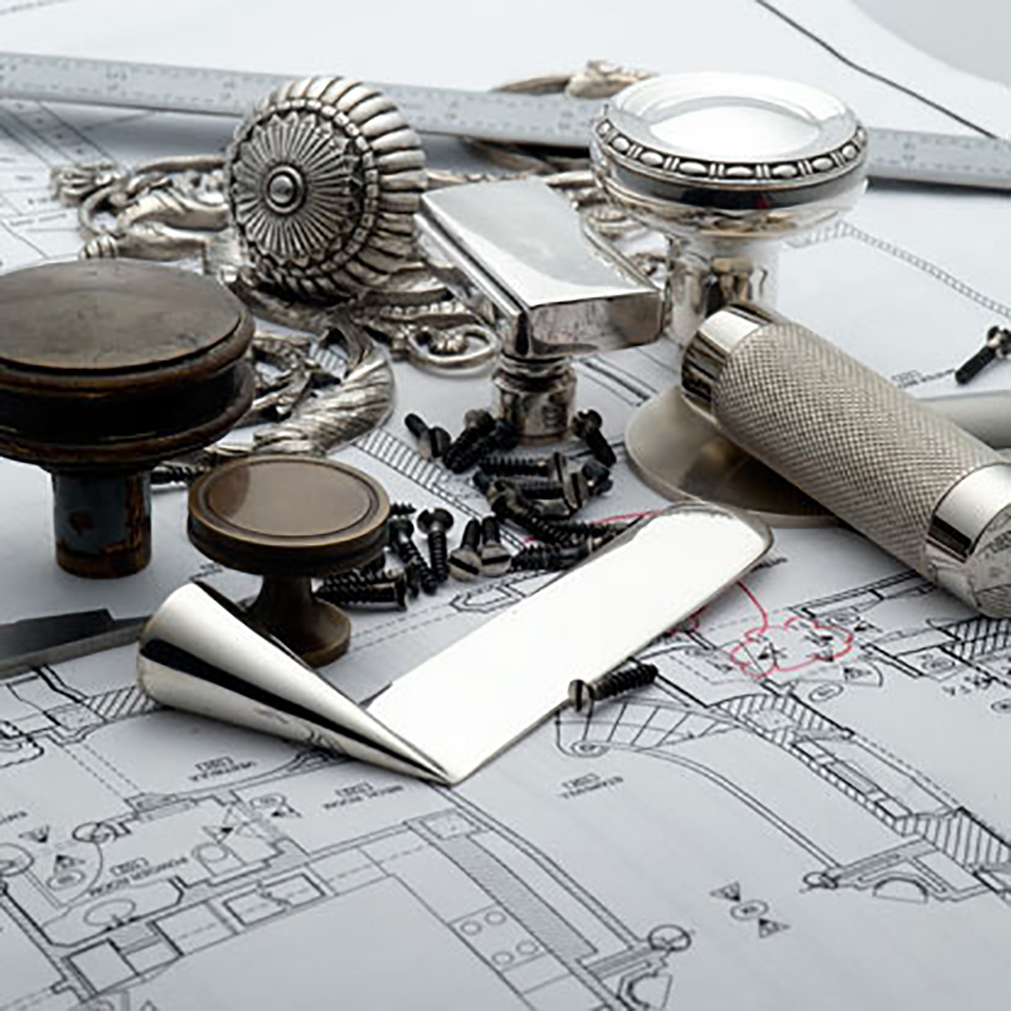
Personalized, Technical Service
From simple counts and door functions, to detailed door and hardware schedules, our technical team of architects, mechanical engineers, and project managers provide detailed, custom proposals and outlines to bring any project to completion. Our engineering team is involved from the beginning—enabling us to anticipate and troubleshoot typical hardware mistakes. H. Theophile's team provides personal, hi-tech service while working with designer and client to create beautiful made-to-order products.
Ordering Process
Projects typically begin with design selections from our web catalog or a visit to our New York showroom. Relevant project information including project name, item and door quantities, finish, and any available architectural documentation (floor plan with coordinating door schedule and door details, etc.) is submitted. Based on this information H. Theophile will provide a pricing quotation and lead time. There is a minimum order requirement of ten doors of hardware or $15,000 for all made-to-order items. Overall production lead times range from 16-22 weeks and require a 50% mobilization deposit.
Lead Times
Because our handles and trims are generally made and finished to order on a project-by-project basis, lead times range from 16-22 weeks. Detailed technical and installation drawings as well as pre-mortise items can be provided earlier in the project to support door and millwork fabrication. Locksets, other mechanisms, and hinges are provided on shorter lead times when possible (6-14 weeks) to facilitate pre-hanging of doors in the millwork shop or on site.
Ordering Process
Projects typically begin with design selections from our web catalog or a visit to our New York showroom. Relevant project information including project name, item and door quantities, finish, and any available architectural documentation (floor plan with coordinating door schedule and door details, etc.) is submitted. Based on this information H. Theophile will provide a pricing quotation and lead time. There is a minimum order requirement of ten doors of hardware or $15,000 for all made-to-order items. Overall production lead times range from 16-22 weeks and require a 50% mobilization deposit.
Lead Times
Because our handles and trims are generally made and finished to order on a project-by-project basis, lead times range from 16-22 weeks. Detailed technical and installation drawings as well as pre-mortise items can be provided earlier in the project to support door and millwork fabrication. Locksets, other mechanisms, and hinges are provided on shorter lead times when possible (6- 14 weeks) to facilitate pre-hanging of doors in the millwork shop or on site.
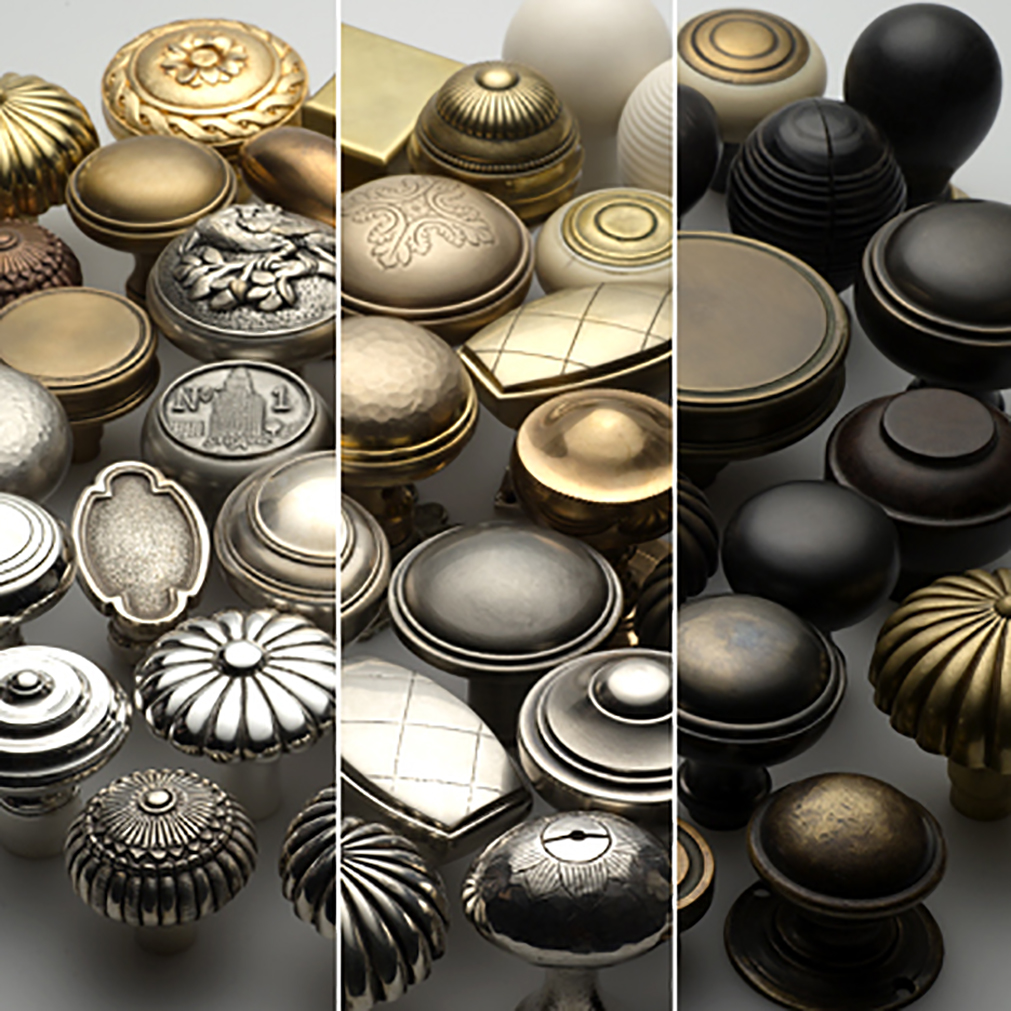
Samples and Finishes
We have a range of signature and custom finishes including polished nickel, antique silver, antique bronze, pewter, statuary bronze, burnished nickel, antique copper, and gunmetal. Our collection also includes a number of limited edition fittings in materials such as Corian, horn, bone, and semi-precious stones.
Our collection of hardware can be seen in person by scheduling a studio visit. If you are unable to visit our New York showroom, samples may be borrowed upon establishing a trade account. Please contact studio@htheophile.com to initiate this process which will include a credit card authorization form.
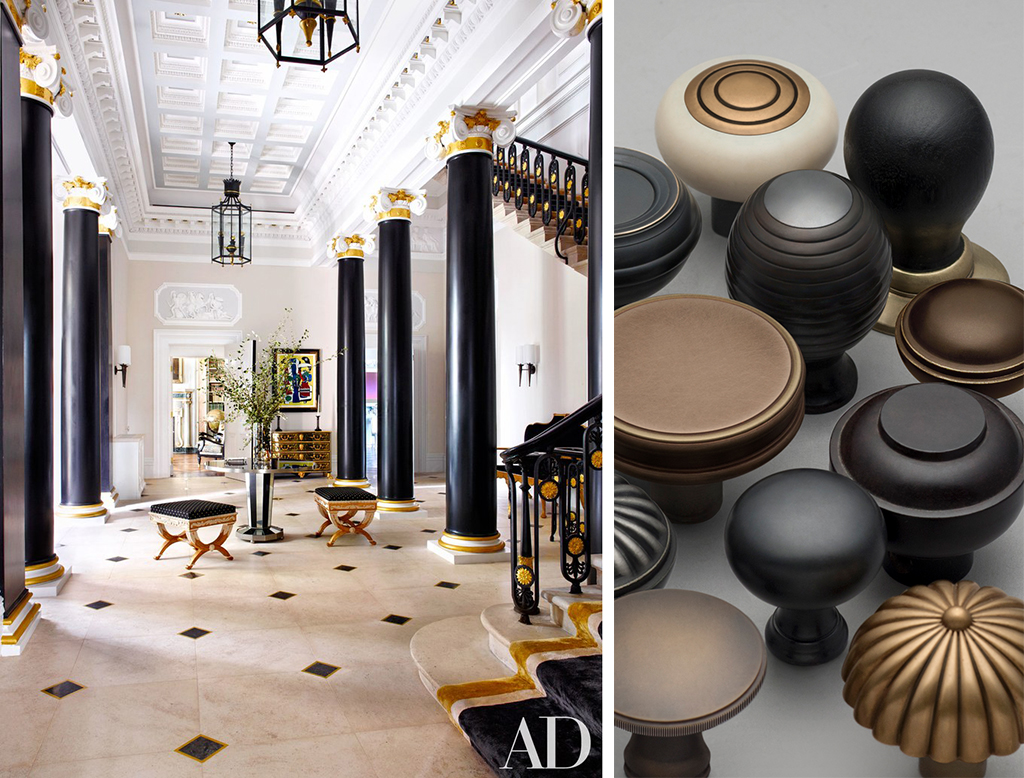
Bespoke Projects
Our studio and sales environment is unique. Our work ranges from new production, to antique and prototype collections, to original designs — all of which can be brought together to develop bespoke hardware schemes. Based on the client's hardware selection, concept ensemble photographs are developed to capture the range and flavor of custom hardware choices, and are accompanied by detailed product documentation.
Technical Review and Submittals
Our team handles the technical review and assessment of complex document packages, and communicates and coordinates with door fabricators, general contractors, hardware installers, designers, and maintenance staff. All of our products are carefully packaged and every single item — from screw to door knocker — is photographed and labeled impeccably to maximize project efficiency on site. We include polishing cloths, handling gloves, and extra screws, when appropriate.
Submittals are prepared for technical review by our team. Our submittals include standard tearsheet product documentation, door-by-door quotations, and custom product documentation. Additionally, technical drawings illustrating placement issues, planning installation diagrams, and coordinating different designs are provided.
Technical Review and Submittals
Our team handles the technical review and assessment of complex document packages, and communicates and coordinates with door fabricators, general contractors, hardware installers, designers, and maintenance staff. All of our products are carefully packaged and every single item -- from screw to door knocker – is photographed and labeled impeccably to maximize project efficiency on site. We include polishing cloths, handling gloves, and extra screws, when appropriate.
Submittals are prepared for technical review by our team. Our submittals include standard tearsheet product documentation, door-by-door quotations, and custom product documentation. Additionally, technical drawings illustrating placement issues, planning installation diagrams, and coordinating different designs are provided.